Switching to preventive maintenance is a strategy that saves time and money and helps operations run more smoothly. For many organizations, maintenance management can account for nearly half of the operational budget.
According to ReliabilityWeb, equipment reliability can increase from 35% to 50% after implementing an efficient CMMS (Computerized Maintenance Management System). Additionally, improving ticket/work order management can increase savings by 5-15%, and optimizing inventory can reduce costs by another 20%.
Reduced Downtime
When it comes to production, the saying “time is money” is true. Every time equipment is stopped for maintenance, you lose money both in employee salaries (since employees must wait for equipment repair) and in products (which cannot be produced during equipment downtime). Preventive maintenance significantly reduces downtime as its primary goal is to prevent it.
Increased Operational Efficiency
When preventive maintenance is properly implemented, equipment is maintained through a routine process, ensuring that it can always run optimally. When machines operate more efficiently, they don’t need as much energy and resources. This means cost savings and an improvement in the environmental footprint.
Reduced High Costs of Corrective Maintenance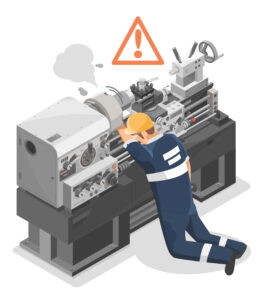
Corrective maintenance is incredibly costly. When something breaks unexpectedly, the following costs occur:
- Costs of your maintenance team (including overtime pay)
- The extra time needed to diagnose the problem
- The cost of replacement parts (including expedited shipping expenses). Preventive maintenance can dramatically reduce the risk of these costs.
Extended Equipment Lifespan
In addition to reducing downtime and costly repairs, preventive maintenance will also extend the lifespan of your equipment. When everything is up to date and functioning correctly, you’ll maximize the lifespan of your machinery, helping you get the most out of your investment.
Improved Customer Service
Customers trust the products or services you offer. They expect them to be delivered on time, and no one wants to hear that products will be delayed due to equipment failures. When you can consistently provide quality services on time to your customers, you’ll have happier customers, better reviews, more referrals, and ultimately, more sales.
Implementing a Preventive Maintenance Program
If you’ve relied on corrective maintenance but want a solution that saves you money, time, and stress, it’s time to switch to preventive maintenance. While an initial investment is required, you’ll end up saving a lot in the long run.
You also don’t have to worry about a complete transition from corrective maintenance to preventive maintenance because the maintenance software platform handles both types. After implementing preventive maintenance software, you can work on configuring equipment one by one on a preventive maintenance schedule. This way, you won’t be overwhelmed, and you can work at your own pace.
Preventive maintenance offers many significant advantages, and in the section below, we’ll discuss improving ROI (Return on Investment).
Calculating Classic Maintenance ROI
If you are familiar with maintenance expenses (including any combination of equipment, inventory, downtime, overtime, or overall costs), the formula is relatively straightforward.
The example focuses on a 3-year period. Annual maintenance budgets are $400,000, or $1,200,000 over the three years. The cost of maintenance software in this 3-year period in this example is $9,150.
Annual percentage improvement estimates are 2%, 4%, and 7% based on the assumption that improvements increase through more efficient use of maintenance software. With these improvement percentages, the company will achieve a ROI of 368% and a payback in just 2.56 months.
Calculating ROI for Reduced Downtime
The key to this model is calculating the average cost per hour when equipment is stopped. For example, if you’re manufacturing a product, and the machine producing it breaks down, you can no longer make that product.
- Costs of lost production
- Payment for the person monitoring this equipment, even if it’s not functioning
- Costs of technicians who need to work to repair the equipment
- Costs of spare parts needed to fix the breakdown
For example, you have 10 production machines, each running for 15 hours a day. Historically, the equipment is stopped 5% of the time. When the equipment is stopped, you spend $100 per hour (downtime per hour).
For this example, the CMMS software cost is $5,000.
Using this data, if you can reduce downtime from 5% to 4.5% – a reduction of just 10% from current downtime levels – the ROI after one year is $22,375.
This is a profit above the software cost. If you could reduce daily downtime to 3.75%, cost savings would be $63,438 per year.
QLEAP KMR is a software platform that helps plan and organize maintenance activities. The system assists users as the web platform can be adjusted and modified according to the factory’s specific needs. The core of the software represents the three general types of maintenance:
- Corrective/Accidental Maintenance involves recording all equipment failures. These can be entered directly, through breakdowns, or through an approval process: reporting the fault, approval-qualification-allocation of technicians, and maintenance resolution.
- Preventive/Planned Maintenance is performed based on a maintenance plan and intervention frequency. For each piece of equipment, the maintenance list is configured according to its periodicity.
- Predictive Maintenance: The IoT module collects data from sensors about vibrations, temperature, flow, etc. These are configured with reference intervals (ranges). If a recorded value falls outside the range, the application can schedule maintenance or send SMS and/or email notifications. The direct retrieval of operating hours from equipment helps in scheduling preventive maintenance based on usage (operating hours).